Automatisierungstechnik
MES | SCADA | HMI | SPS
Mit unseren innovativen Produkten und Lösungen bieten wir Antworten auf alle Fragen der industriellen Automatisierungstechnik, MES, SCADA, HMI und SPS. Als unser Partner profitieren Sie von unserer langjährigen Erfahrung im Bereich der Automation – von der Planung über Engineering, Installation, Inbetriebnahme und Schulung bis zu Service und Support.
Wenn Sie sich für industrielle Automatisierungslösungen interessieren, sind Sie bei uns genau richtig.
GIP steht für durchdachte, effiziente und innovative Automationslösungen für industrielle Produktionsanlagen.
Überzeugen Sie sich selbst.
Automatisierungstechnik mit MES-Software
Wir sind ein international tätiger Anbieter effizienter Automatisierungslösungen für die Fertigungs- und Verfahrensindustrie. Zur Realisierung hochwertiger Prozess- und Fertigungssteuerungen liefern wir komplette Automatisierungskonzepte aus einer Hand.
Das heißt konkret:
Wir erstellen Neuanlagen, führen Modernisierungen durch und sind von Anfang an beratend tätig.
Als ein innovatives Unternehmen sind wir erfahren und kompetent in der Prozessautomation, erfolgreich im Wägen, Dosieren und Fördern von festen und flüssigen Medien für den kontinuierlichen Betrieb, und stark im rezeptgetreuen Herstellen von Gemengen in Batch- und Kontianlagen. Top-Spezialisten arbeiten an modernster Automatisierungstechnik, MES-Systemen und Prozessleittechnik mit Steuer- und Lastebene, sowie dem kompletten Engineering.
Diese Ansprüche sind die Basis in der Entwicklung unseres hauseigenen Produktionsleitsystems VarioBatch®.
VarioBatch® umfasst alle Bereiche eines Produktionsbetriebes von der Rohwarenannahme über die Produktion bis zum Versand sowie einer Kommunikation mit PPS-, LIMS- und ERP-Systemen. Das System kann weitestgehend konfiguriert und parametrisiert werden. Es zeichnet sich durch eine schnelle Anpassungsfähigkeit an die individuellen Bedürfnisse aus.
Unsere Kernkompetenzen
- Erstellen kompletter Automatisierungslösungen, von der Feldebene bis zum MES (Manufactoring Execution System) mit Ankopplung an SAP oder anderen ERP-Systemen.
- Automatisches Wägen, Dosieren, Fördern von festen und flüssigen Medien sowie rezeptgetreuem Herstellen von Gemengen in Batch- und Kontianlagen.
- HMI und SCADA Anlagenvisualisierungen für die Leitwarte und auch direkt an der Maschine.
Unsere Dienstleistungen
- Entwicklung von Leitsystemen (MES und PLS)
- Programmierung von SPS-Steuerungen (PLC)
- Erstellung von Visualisierungen (SCADA)
- Planung und Liefern von Hard- und Softwaresystemen für den Produktionsprozess
- Schaltschrankbau und Verkabelung
Unsere Kunden
- Anlagenbauer
- Ingenieurbüros
- Anlagenbetreiber
Wir gehen mit Ihnen ein strategisches und partnerschaftliches Verhältnis ein. Sie profitieren von unserer langjährigen Erfahrung und unserer ausgewiesenen Fachkompetenz.
Wenn es um die Lösung Ihrer Aufgaben geht, sind wir schnell und flexibel. Unabhängig davon, ob es sich um Änderungen, Störungsbehebungen in Ihrer Anlage oder einfach nur um kleine Hilfestellungen bei Problemen rund um Ihre Anlage / Ihr System handelt.
Dies konnten wir nur mit hochmotivierten und an den Unternehmensentscheidungen beteiligten Mitarbeitern erreichen.
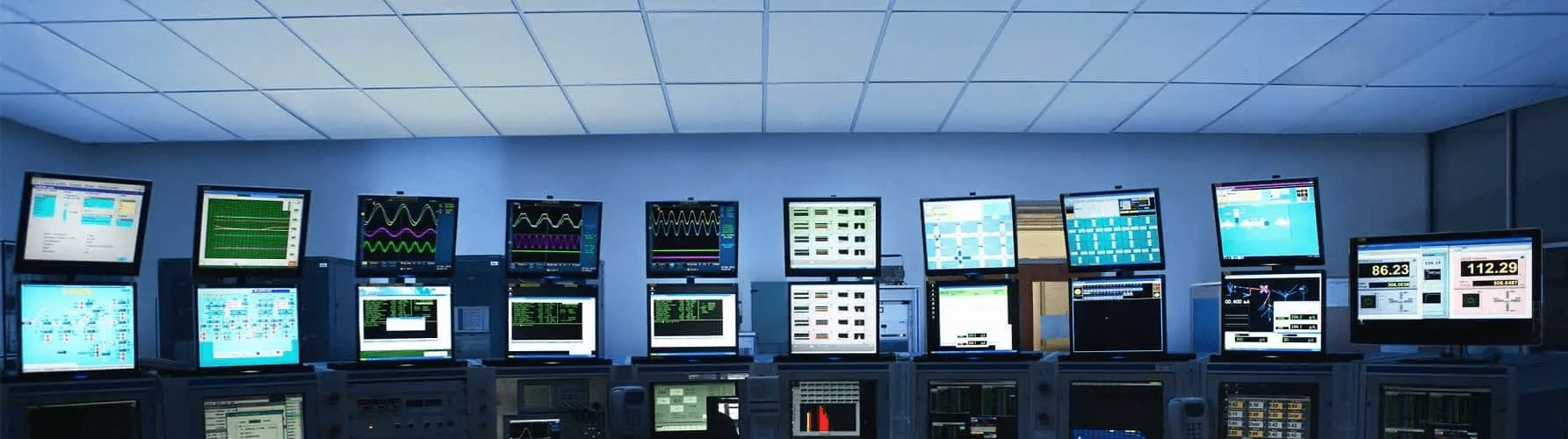

Folgen Sie uns: